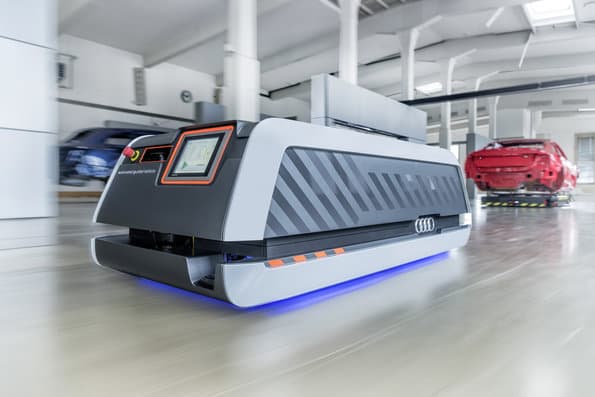
In Anbetracht der technischen Entwicklungen der letzten Jahrzehnte, kann der Fortschritt schon lange nicht mehr mit der Behäbigkeit einer Schnecke verglichen werden. Mit dem immer effektiverem Einsatz von Maschinen wird der Mensch in seiner Unvollkommenheit unterstützt, seine Arbeit somit zu etwas transformiert, das an ein durch Perfektion und Präzision ausgezeichnetes Ideal grenzt. Die Automatisierung der Montageprozesse profitiert ständig vom technischen Fortschritt.
Jedes Jahr entwickeln sich mehr Möglichkeiten, die Visionen verwandeln sich in Projekte und Prototypen, später entstehen daraus Standardlösungen.Manche Innovationen geben bestehender Technik mehr Raum für Erweiterungen, andere zeigen neue Richtungen und nehmen den bewährten Lösungen den Wind aus den Segeln.
Die Automobilindustrie liefert uns dafür genügend Beispiele.
Smart Factory
ist wohl eine der spektakulärsten.
Mit der Einführung des Fließbandes hat die Industrie vor vielen Jahren einen Riesenschrittgewagt und die Massenfertigung ermöglicht. Das hat Einfluss auf viel mehr als Produktionszahlen und Produktionsprozesse, und ist in der Kultur von Industrienationen fest verankert. Nun ist allerdings diese Produktionstechnologie nicht mehr immer zufriedenstellend. Mit der Innovation der ‚Modularen Montage‘ läuft es darauf hinaus, dass die Arbeit am Fließband irgendwann der Vergangenheit angehört.
Audi bereitet sich den Weg für die Modulare Montage.
Auf die Einführung der modularen Montage und den kompletten Verzicht auf das gute alte Fließband sind auch die innovativsten Betriebe noch nicht ganz vorbereitet. Die wichtigsten Bausteine dieser Technologie sind aber bereits gelegt.
Audi testet bereits in Gör ihre ersten FTS (Fahrerlose Transportsysteme). Nutzung von Big Data und Zusammenarbeit von Mensch und Maschine funktioniert bereits im laufenden Betrieb.
Flexible Verschraubung mit LBRinline
Manche Montageprozesse gelten vom Anfang an als ergonomisch schwierig. Dazu gehören in erster Linie die Arbeiten unter dem Fahrzeugboden.
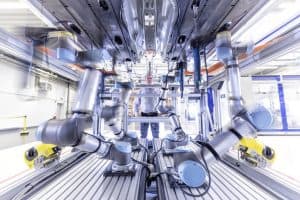
Die Montage des neuen Audi A3 Sportback e-tron fordert, aufgrund seiner gesteigerten Komplexität, besondere Aufmerksamkeit.
Das Schraubmuster der Unterbodenverkleidung ist hier etwas anders als bei anderen Modellen.
Um für mehr Flexibilität innerhalb der Verschraubung zu sorgen, setzt der Automobilkonzern einen Montagewagen ein, der mit einem LBRinline (Leicht-Bau-Roboter in der Linie) optimiert wurde.
Der mit 14 Schraubern ausgestattete Aluminium-Montagewagen wird vom Mitarbeiter über Zapfen an die Gehängebahn angekoppelt. Während einer 20-sekündigen Begleitfahrt, verschrauben die vier LBR die neuartige Unterbodenverkleidung des Plug-in-Hybrids vollkommen eigenständig.
Drei Laserscannern sorgen derweil für die Sicherheit der Mitarbeiter und stellen sicher, dass ein direkter Kontakt zwischen Mensch und Maschine vermieden wird.
Obwohl jeder Roboter nur 18 Kilo schwer ist, könnte eine Kollision schlimme Folgen haben.
Die LBRinline können nicht nur eine schnelle und ergonomische Verschraubung gewährleisten, sondern soll zukünftig auch an andere Arbeitsschritte angepasst werden. So verschafft Audi sich immer mehr Spielraum für mehr Flexibilität innerhalb der Produktion und unterstützt seine Mitarbeiter tatkräftig in der Montage. Bei jährlich rund 500 Millionen Verschraubungen allein im Audi-Werk Ingolstadt, ist dies eine lohnenswerte Innovation.
Überwachte Verschraubungen liefern wichtige Informationen
Jedes Audifahrzeug setzt sich aus durchschnittlich 1000 Schrauben zusammen, welche mit Überwachung der Schraubparameter eingedreht sein müssen. Das sind jede Menge nützlicher Daten, welche nicht nur kontrolliert, sondern auch gespeichert werden.
Diese Informationen finden als Teil der Big Data für viele Prozesse Verwendung.
Dabei handelt es sich um ein Verfahren, bei dem anonymisierte Verschraubungsdaten ausgewertet werden. Die Auswertung der Schrauberdaten wird durch die Schrauberdaten-Analyse zum Frühwarnsystem für mögliche Fehler.
Im Bereich der Automobilmontage werden, durch die Nutzung von Big Data als Lieferant für wertvolle Auswertungsdaten, nun immer präzisere Messungen möglich, die ihrerseits Anstoß für neue Entwicklungen geben.
Die verwendeten Schrauber überprüfen kontinuierlich die Messwerte von Drehwinkel und Drehmoment. Bei einem NIO-Schraubprozess, z.B. durch Späne im Schraubgewinde, reagiert das System mit automatischem Abbruch des Schraubprozesses. Obwohl sich diese Reaktion um nur wenige Sekunden verzögert, streben die Audi-Entwickler nach mehr. Denn die Nutzung der Big Data ermöglicht in meisten Fällen die Voraussage von solchen Problemen innerhalb der ersten 0,3 Sekunden des Schraubprozesses.
Mit solcher Art Entwicklungen gelingt es dem Team des Audi Production Labs immer wieder eine Effizienzsteigerung zugunsten des Produktionsprozesses zu erzielen.
Das Zusammenwirken vom geistigen Anteil des Menschen mit dem rein Maschinellen des Roboters, bringt in der Fusion Neuigkeiten hervor, die die Zukunft der Technik maßgebend beherrschen werden.
Quelle Bilder und Informationen: Audi
Wichtige Bezugsquellen finden Sie in der Kategorie Montage- und Schraubtechnik.
Hinterlasse jetzt einen Kommentar