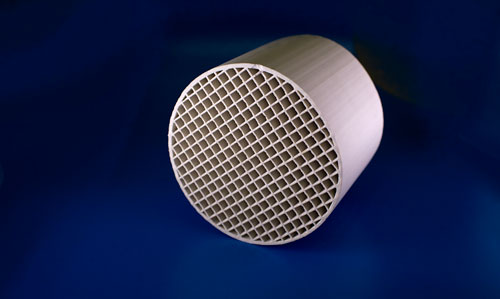
Porzellanfabrik Hermsdorf
Vielfalt an technischen Lösungen ist auf der Hannover Messe seit Jahren ein vertrautes Bild. Die Messe liefert dem Besucher nicht nur viele Informationen, sondern auch eine gewisse Vorstellung bezüglich der Entwicklungstrends in der modernen Technik.
Einer dieser Trends trägt das Label Losgröße Eins oder bedient sich des benachbarten Begriffs Individualisierung.
Beide Stichwörter beziehen sich auf die automatisierte Welt, die gerade ihren ersten Schritt weg vom Produktionsband wagt. Umso überraschender war für uns das Geschäftsmodell eines Herstellers der Hochleistungskeramik aus Hermsdorf.
Bezahlbare Einzelstücke in manuellem Vorgang
„Wir entwickeln die Materialien nach eigenen Rezepturen und verwenden keinerlei Organik“, berichtet die Geschäftsführerin und Inhaberin Frau Kaiser. „Die Fertigungstiefe ist bei uns sehr hoch. Nur die Rohstoffe werden angeliefert, danach übernehmen unsere Mitarbeiter.
Unsere technische Keramik ist sehr sauber. Auch die Plastizität der Masse für die Formgebung erreichen wir mit natürlichen Stoffen wie Ton – ohne organische Zusätze. So entsteht wenig Umweltbelastung und die Produkte sind für die Pharmaindustrie, Dentaltechnik oder Lebensmittelindustrie freigegeben.
So wird zum Beispiel unsere Hochleistungskeramik für die Herstellung von Trommeln eingesetzt, mit denen Müsli für Allergiker gemahlen wird. Oft verwendet man in der Lebensmittelindustrie Edelstahltrommeln mit Chrom-Nickel-Legierung. Doch dadurch kann die häufigste Form von Kontaktallergien provoziert werden – die Nickelallergie.
Das Problem kann durch die Anwendung unserer Keramik gelöst werden. Denn sie besteht nicht nur aus einem unbedenklichen Material, sondern ist auch vollkommen abriebfest. Bei dem mechanischen Kontakt mit dieser Keramik gelangen keine Fremdpartikel in das Endprodukt“.
Diese Art von Produkten wird in Hermsdorf manuell in Kleinserien produziert. Die plastische Herstellung solcher Mühlen dauert zwei Tage, danach folgt die Trocken-Zeit von etwa 16 Wochen, erst dann kommt das Glasieren, Brennen etc.
Und trotzdem schafft es die Porzellanfabrik, bezahlbare Einzelstücke in manuellem Vorgang herzustellen.
Die gut durchdachten Produktionsprozesse können auch bei Handarbeit sehr effektiv sein.
Oft bedeutet ein Produkt = ein Kunde, denn es wird sehr viel im Kundenauftrag und völlig projektbezogen entwickelt.
Doch das heißt nicht, dass es in der Porzellanfabrik keine automatisierten Produktionsprozesse gibt. Da wo es Sinn macht, (wie z.B. bei der Produktion der Waben für Wärmetauscher) wird automatisiert.
Je nach Produkt und Kundenanforderungen werden unterschiedliche Materialien eingesetzt: Aluminiumoxid, Ton, Kaolin, Siliciumcarbid, Steatit usw. Es wird gegossen, extrudiert, plastisch geformt. All diese Prozesse haben sich längst bewährt. Das eigentliche Knowhow steckt in dem gezielten Tuning der Keramikeigenschaften.
Innovative keramische Beschichtung und Ressourceneffizienz
Korrosions- und temperaturbeständig, dehnbar, leicht – der Titan ist ein populärer Rohstoff, welcher nicht gerade billig ist. Bei der zerspanenden Bearbeitung dieses wertvollen Materials gehen viel Energie und Werkstoff verloren. Um das zu vermeiden, werden heute viele Titanteile im Gießprozess hergestellt.
Aber auch dieser Prozess hat seine Tücken. Beim Titangießen treten oft Probleme auf, wie das Kleben von Schmelze am Tiegel. Die Oberfläche des Tiegels wird dabei vom geschmolzenen Titan angegriffen und zu einem zunehmenden Störfaktor.
Zusammen mit einem Kunden hat die Porzellanfabrik Hermsdorf ein neues BeschichtungsmMaterial entwickelt. Dieses schützt die Innenseite des Tiegels und verhindert die Anhaftung der Schmelze.
Hinterlasse jetzt einen Kommentar