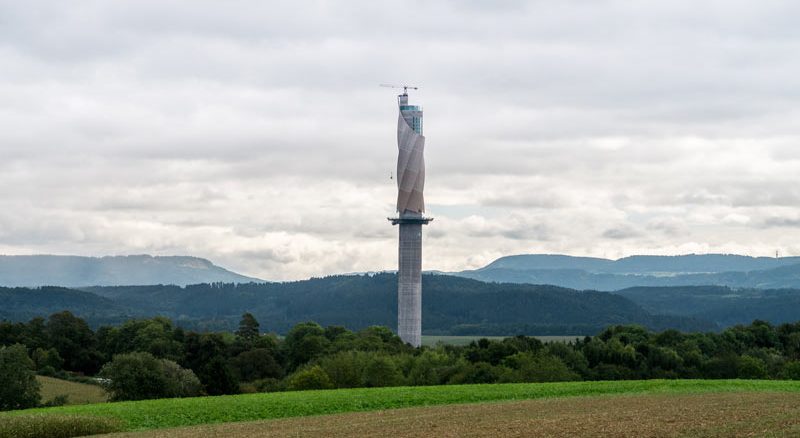
Jede neue Technologie muss zuerst auf die Probe gestellt werden. Eine Testumgebung zu schaffen stellt oft eine nicht zu unterschätzende Herausforderung dar.
In diesem Herbst geht in Deutschland ein spektakuläres Projekt in die heiße Phase. Schauplatz – das schwäbische Rottweil. Der Testturm Rottweil erstreckt sich ganze 246m in die Höhe und ist somit die höchste allgemein zugängliche Besucherebene in Deutschland. Das macht ihn nicht nur zu einer Touristenattraktion – der Turm hat auch seine ganz spezielle Mission in der Welt der neuen Technologien. Denn bald werden hier die innovativsten Schnellaufzüge wichtigen Sicherungstests unterzogen. Die auch als „TyssenKrupp-Testturm“ bekannte Konstruktion wiegt stolze 40 000 Tonnen. Der Testturm besitzt zwölf Schächte, in denen z.B Aufzüge für Wolkenkratzer getestet werden können. Die Schächte sind für Fahrgeschwindigkeiten von bis zu 18 m/s konzipiert. Für solche Leistungen gibt es auf der ganzen Welt mehr als genügend Kunden.
Am 22.06.17 stellte TyssenKrupp selbst den weltweit ersten seillosen Aufzug vor. Mittlerweile besitzt der Testturm drei Schächte für die Tests solcher Aufzüge.
Der MULTI hat praktische Vorteile. Statt reinen Auf- und Abfahrten einer Kabine, ermöglicht er eine unabhängige Zirkulation vieler Kabinen, ähnlich wie bei einem U-Bahnsystem in einem Gebäude. Die Kabinen, die ohne Seil betrieben werden, verfügen über ein redundantes, kabelloses EDV- und Energiemanagement. Geschützt werden sie durch ein mehrstufiges Bremssystem.
Ein hervorragender Membranbau der Fassade sorgt für eine ausgefallene Ästhetik der Konstruktion. Um das Material dafür bis nach ganz oben transportieren zu können, entwickelten Ingenieure ein spezielles Montagegefährt. Drei Triebstockschienen ragen 210m nach oben und ermöglichen so einen sicheren Transportweg. Eine Spiralkonstruktion aus sechs Rohrzügen hält das Membrangewebe zusammen.
Der Koloss kann sich durch ein interessantes Design durchaus sehen lassen. Der Stahlbeton des Turmschaftes ist von einer Glasfasergewebehülle umgeben, die zur Spitze hin immer mehr Transparenz aufweist. Abhängig von der Tages- und Jahreszeit ergeben sich Veränderungen in der Außenmembran und durchfluten die Innenräumen unterschiedlich stark mit Sonnenlicht. Die Verkleidung besitzt selbstreinigende Funktion und bietet gleichzeitig Schutz vor Wettereinflüssen, wie starkem Wind, Hitze oder Auskühlung. Die Fassade wurde von der Firma „Tayio Europe GmbH“ an den Turm angebracht.
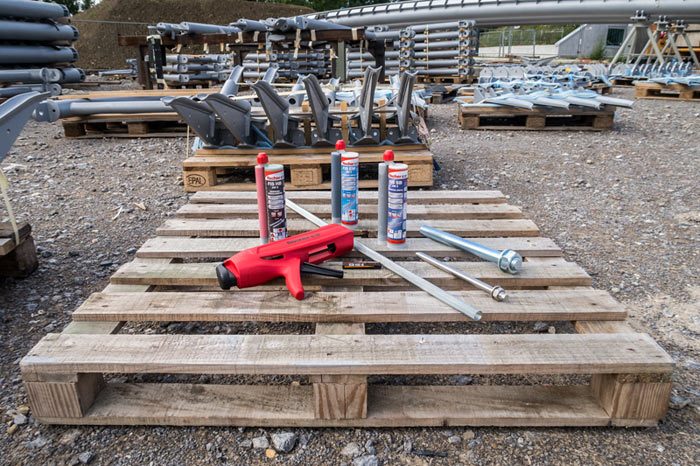
Durch eine Stahlkonstruktion ist die Verbindung der Fassadenbekleidung mit dem Betonbau gewährleistet. Ankerplatten, Seile, Stahlröhre und jede Menge Schwerlastbefestigungen waren für den Zusammenhalt nötig. Die Metalldübel zur Verankerung im Beton müssen der europäischen Leitlinie ETAG 001 entsprechen. Als Lieferant für solche Befestigungen wurde die Firma „Fischer“ ausgewählt. Keine unwichtige Rolle spielte dabei auch die Montagefreundlichkeit. Vom Fuß des Turmes bis auf eine Höhe von 27m, kamen die Ankerstangen FIS A M20x320 aus Edelstahl (A4) zum Einsatz. Um höchste Tragfähigkeit zu gewährleisten setzten Konstrukteure den Epoxidharzmörtel FIS EM 390 S ein. Ab einer Höhe von 27m und aufwärts wurde das Verbundankersystem „Powerbond“ mit einem M16-Durchmesser in A4 für die Befestigung verwendet. Wichtig waren dabei kurze Aushärtezeiten und eine sehr hohe Zugtragfähigkeit. Die Ankerstangen (FIS A M16x250 A4) sitzen im Beton „nur“ 180 mm tief, was für den Ausmaß der Konstruktion nicht gerade viel ist. Daher ist es wichtig, dass das Befestigungsmaterial qualitativ hochwertig ist. Zwischen 110 und 207m kommt das Verbundankersystem „Superbond“ in Kombination mit den Ankerstangen RG M 16×300 A4 zum Einsatz.
Hinterlasse jetzt einen Kommentar